Processo Cadeia de Ajuda
"É uma rotina com a interação e envolvimento entre as pessoas para se resolver um problema quando ele surge, iniciando-se pelo operador da produção"
"Envolve as lideranças imediatas e os responsáveis de todas as áreas de apoio, com ferramentas e métodos padronizados, para eliminar as instabilidades do processo"
ETAPA 1: CONDIÇÃO PARA DETECÇÃO DE PROBLEMAS
(QUADRO KANRIBAN & MATRIZ DE TREINAMENTO)
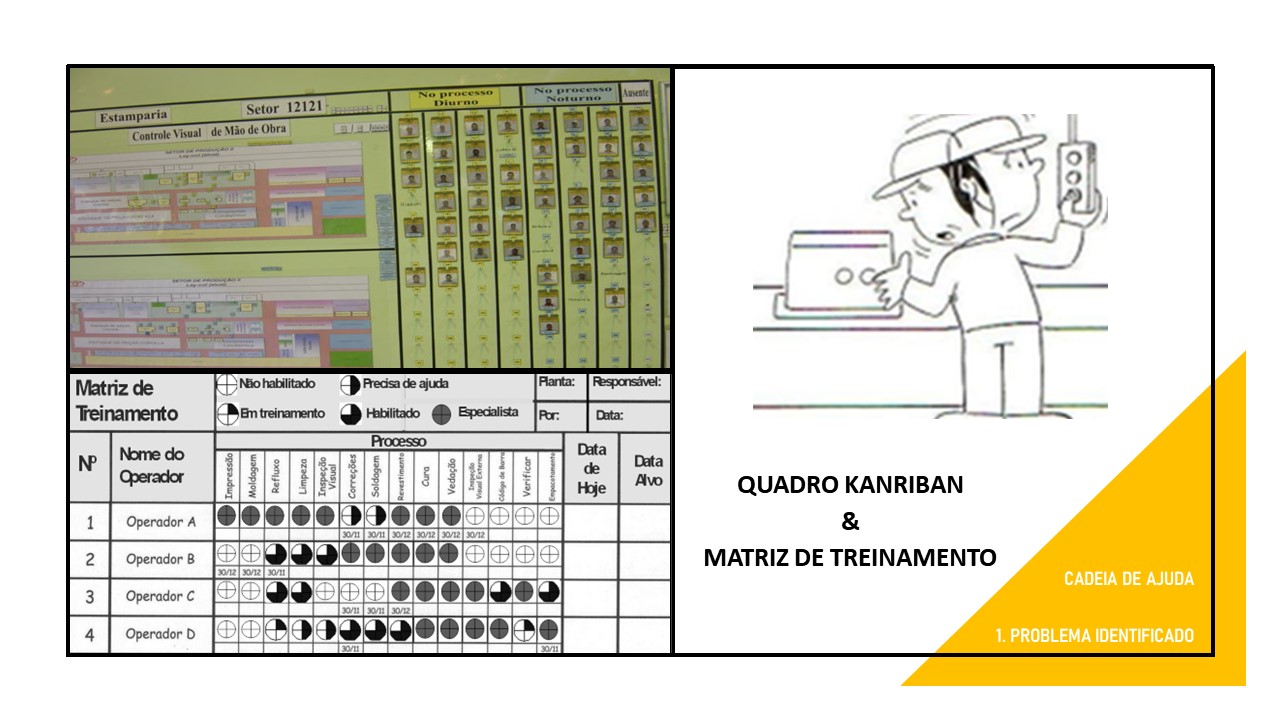
Um processo capaz é aquele que de maneira simplificada e automática detecta os problemas quando eles ocorrem e melhor que isso, antes que eles aconteçam (prevenção).
A Cadeia de Ajuda tem como ponto inicial a capacitação e treinamento constante de seus colaboradores, pois quanto mais eles conhecem o produto e o processo, mais condições eles têm para contribuir com a detecção. Treinamento constante é um dos segredos mas não é a única ação importante, saber onde "escalar" os colaboradores para cada posto de trabalho em específico também contribui para essa rápida ação.
Abuse da gestão visual, quanto mais simples e visual for mais fácil se torna o processo.
ETAPA 2: INFORMAÇÃO DO LOCAL ONDE O PROBLEMA ESTÁ OCORRENDO
(ANDON & "PARAR" O PROCESSO)
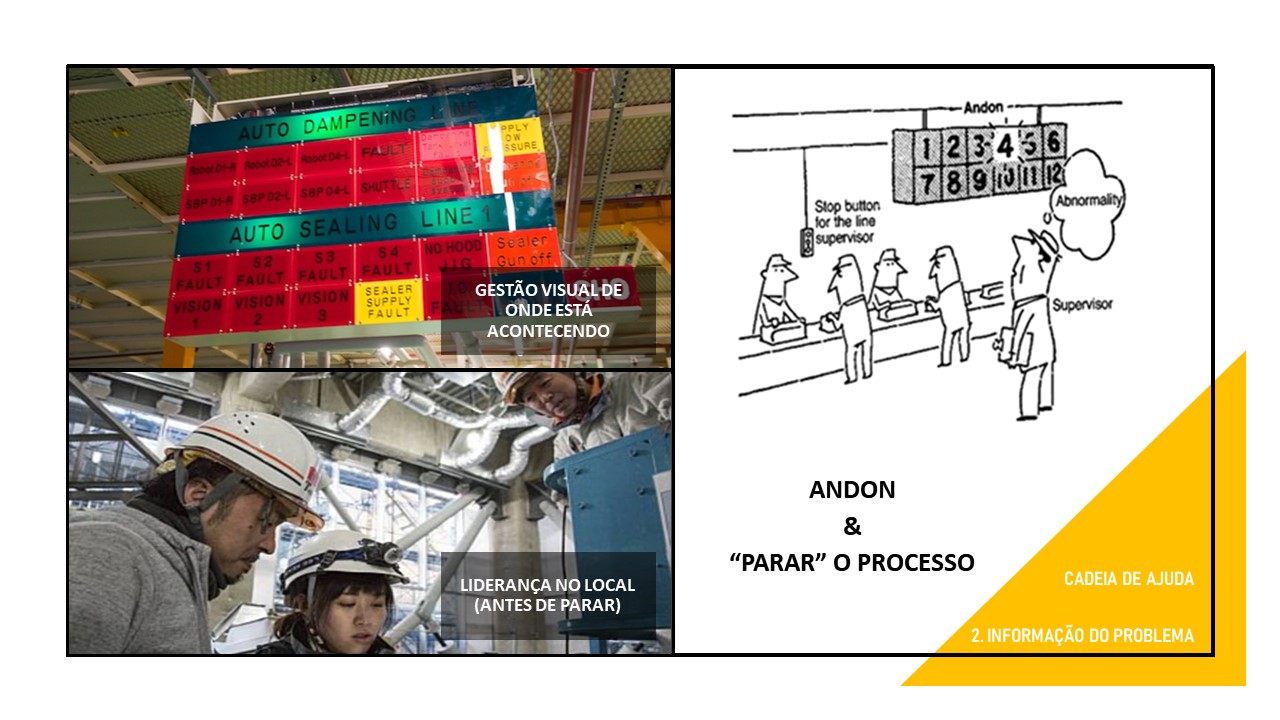
Com os colaboradores treinados e aptos para trabalhar no seu posto de trabalho, a Cadeia de Ajuda se inicia quando alguma anormalidade acontece, seja ele afetando a segurança, a qualidade, a produtividade ou outro fator.
Na iminência de uma "causa raiz" aparecer, o colaborador deve rapidamente "invocar" os 5 Porquês, achar a causa ou no mínimo conter o problema. Por esse motivo quanto mais ele conhecer o produto, o processo e as ferramentas de análise (7 ferramentas da Qualidade), melhores resultados teremos.
Caso ele não consiga, a liderança deve ser acionada e com o auxílio do "Andon" chegar rapidamente ao local para apoiar o colaborador. Se mesmo assim o problema não for contido, aí teremos a "parada" do processo até que se identifique e a causa raiz e um "Kaizen" seja executado.
ETAPA 3: APOIO DA LIDERANÇA
(MECANISMO DE CONTENÇÃO + ISHIKAWA/5 PORQUÊS + QUADRO KAMISHIBAI)

Durante o apoio da liderança imediata, a tratativa do problema deve ser feita com ferramentas de analise simplificada, tais como o Gráfico de Ishikawa e os 5 Porquês.
Nesse momento a agilidade dos colaboradores e da sua liderança são essenciais para encontrar a causa raiz, pois são ferramentas eficientes para a maioria dos problemas do dia a dia.
Achado a causa raiz, o planejamento e a execução da sua contramedida deve ser visualizada pelo Quadro Kamishibai, onde os vários setores de apoio devem ter um "Genba" implementado para com a menor frequência possível para imediatamente constatar a ação e executá-la.
ETAPA 4: PROBLEMA ANOTADO
(MECANISMO DE CORREÇÃO + QUADRO MISSA + DOCUMENTO A3)
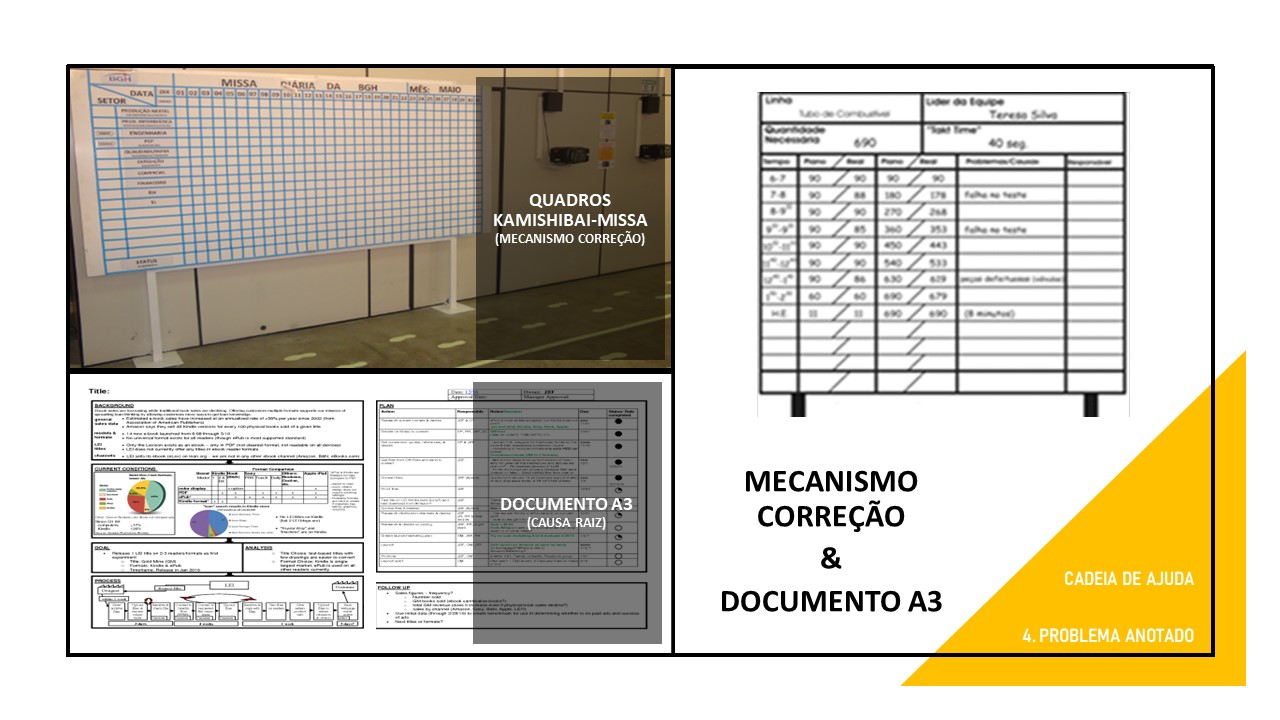
Quando o problema foi contido (não parou a produção) mas não foi identificado e nem eliminado a causa raiz, ou o problema não foi resolvido e nesse ponto a parada da produção é obrigatória para trazer o "senso" da urgência (mesmo que isso não agrade a todos), a reação é necessária para achar a causa raiz.
De maneira corretiva tudo o que não foi "sacramentado" no Kamishibai deve ser revisto, seja um prazo não atendido ou uma contramedida sem eficiência. Um replanejamento da contramedida torna-se necessário através de um realinhamento feito com a presença de todas as áreas (representantes) e das lideranças envolvidas. Esse momento é conhecido como "Missa", pois tudo o que não deu certo é visto diariamente com disciplina e sem achar "culpados". Um quadro com todos os dias do mês e todos as áreas envolvidas serve como auxílio visual (Quadro da Missa) e referência.
Para as contramedidas sem eficiência pode ser necessário a elaboração de um Documento A3, pois uma análise mais detalhada (PDCA) pode ser a solução para o simples mas eficiente"5 Porquês.
A anotação de dados no QAP se torna importante mesmo que seja para consultas futuras (Mecanismo de Prevenção).
ETAPA 5: ATUAÇÃO DO GRUPO MULTIDEPARTAMENTAL
(MECANISMO DE PREVENÇÃO)
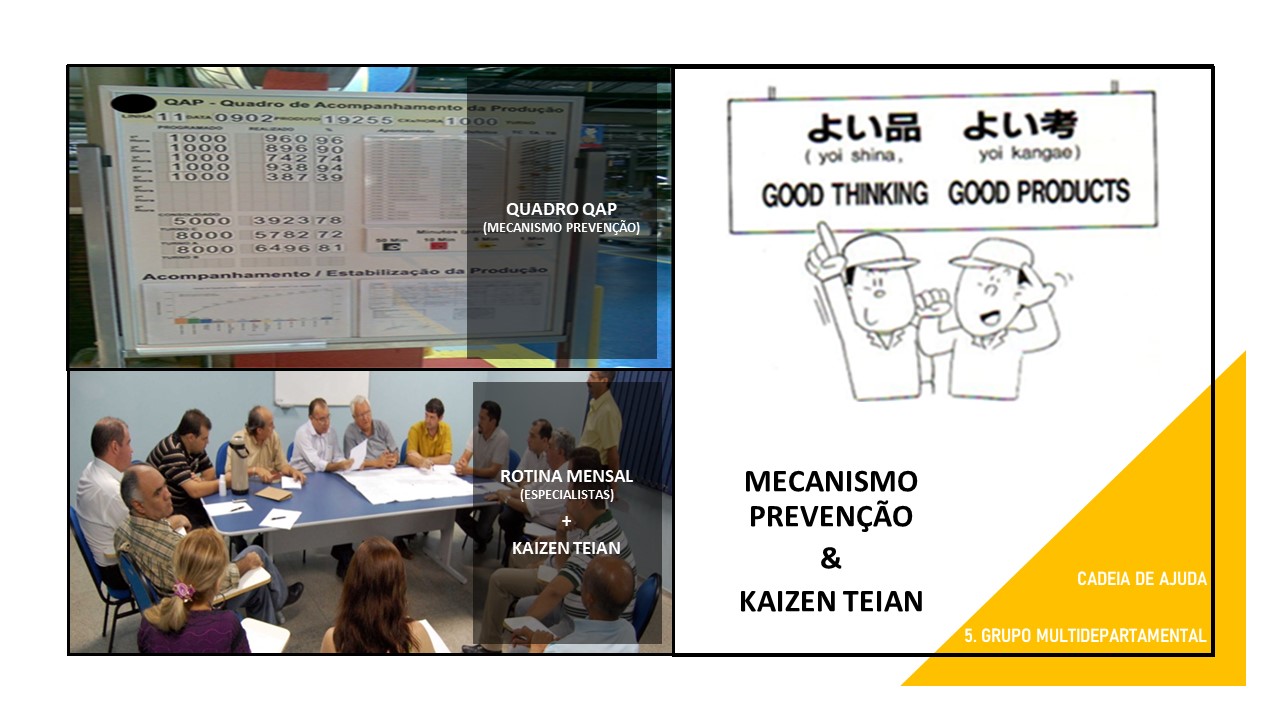
Com os mecanismos de "Contenção" e "Correção" atuando de maneira sistêmica e disciplinada, onde o foco sempre é encontrar a causa raiz dos problemas identificados no QAP, chega o momento que precisaremos dar atenção as anormalidades de pouco impacto e repetitivas pois acumuladamente podem gerar grandes perdas.
Com frequência semanal ou mensal, a liderança da área deverá quando necessário acionar uma equipe de especialistas (Grupo Multidepartamental) para rastrear o histórico no último mês. Elaborando um gráfico de pareto, atacar no mínimo as causas que geram 50% das perdas não solucionadas e, através do Documento A3 estabelecer um plano de ação. Todo esse movimento deve ser realizado até o próximo período e de maneira contínua.
Entendemos que essa prática deverá fomentar muitas contramedidas de pequeno porte (Kaizens) a serem realizadas até por colaboradores do nível operacional, devendo haver a devida valorização desses esforços.
No final das contas os mecanismos de "Contenção", "Correção" e "Prevenção" gerarão pequenos, médios e grandes Kaizens que atuarão na causa raiz da maioria dos problemas levantados no QAP, movimentando programas institucionais de reconhecimento e valorização "de quem faz Kaizens". Esses programas são conhecidos como "Kaizen Teian" (pequenos Kaizens), "Círculo de Kaizen" ou "Kaizens Direcionados" (médios Kaizens) e "Jishiken" (Kaizens da alta liderança).